锂离子电池因其高能量密度、低自放电率和长服役寿命已经成为手机、电动汽车和储能电站等应用的首选。如图1所示的Tesla Roadster电动汽车,其电池包由6831个18650锂离子电芯组成,实现了锂离子电池应用的重大突破,也引发了人们对电池热电管理技术的关注。
图1 以18650锂离子电池为动力的Tesla Roadster电动汽车
锂离子电芯在使用过程中会出现电荷不平衡及电芯电量利用不充分的问题,通常电池组需要配备电池管理系统(BMS)以监控电池的荷电状态(SOC)、健康状态(SOH)等参数并优化其运行。随着BMS的成熟,人们更关注锂离子电池包的热管理技术,这是因为电池温度过低、过高或温差过大,均会缩短电池寿命,而且高温还有可能引发安全事故。
电池热管理系统(BTMS)具有冷却电池、加热电池和缓解电池热失控等功能,可将电池包温度控制在25~40℃,并且单体电池之间的温差小于5℃。锂离子电池对温度十分敏感,当温度低于0℃时,电池容易出现老化、容量衰减等问题,如广泛应用于储能电站的磷酸铁锂电池,其电子与离子电导率在低温下显著下降。
锂离子电池可通过内阻产热机制来升高温度,如自加热、脉冲加热、交流电加热技术等。总体来说,电池加热较易实现,而热量的散出往往需要借助外加设备,因此热管理技术中的冷却技术起着更为关键的作用。
在高温环境下,电池的整体性能不仅会下降,甚至还会导致热失控和爆炸等安全事故,因此,及时排出热量是非常关键的。现阶段电池冷却技术还未十分完善,需要在提高散热性能和均温性以及降低成本等方面进一步优化。
基于目前锂离子电池热管理技术的研究,本工作对几种主流的电池热管理技术进行了详细讨论,即空气冷却、液体冷却、相变材料冷却(PCM)和热电冷却技术,分析了这几种技术的优缺点和实际应用情况,并对锂离子电池的产热模型进行了简单阐述,最后指出了这几种电池冷却技术的未来发展方向。
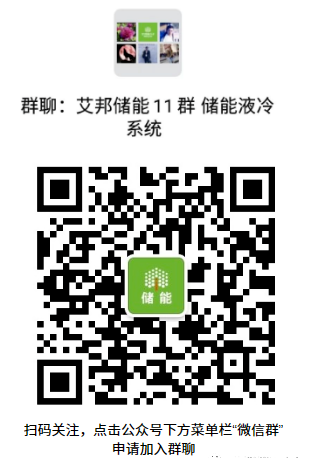
一、锂离子电池热管理技术
锂离子电池作为全球动力电池、储能电池和消费电池领域的主流电池,其热管理技术的发展一直备受关注。
早期的锂离子电池热管理系统较简单,主要是通过空气自然对流降温,即被动式空气冷却。后来增加了风扇等加快空气流动或利用冷风水槽提前对空气进行冷却,即主动式空气冷却,冷却效果得到了改善,但是噪声较大且均温性不好。
为解决该问题,研究人员发明了液体冷却技术,包括冷却板液冷和浸没式液冷。其中冷却板液冷技术发展较为成熟,具有较好的冷却效果,但容易出现冷却液泄漏等问题,从而造成安全隐患。
浸没式液冷是近几年迅速发展起来的冷却技术,冷却效果明显,但对冷却液要求较高。相变材料冷却和热电冷却技术是近年来发展起来的新型冷却技术,没有移动部件,结构简单,但是制冷效率低。
总体来看,现阶段的冷却技术均存在优缺点,一般情况下需要结合两种或多种冷却技术对电池进行复合式冷却,下文中对上述锂离子电池冷却技术进行了更详细的阐述。
空气冷却一般分为自然冷却和强制冷却两种,利用空气流动带走电池产生的热量进而冷却电池,具有结构简单、成本低、无污染的优点。
自然冷却是一种被动式的冷却方式,往往只需要设计散热风道,在早期的锂离子电动汽车中应用广泛,如图2(a)中采用空气自然对流冷却电池的Nissan Leaf。但是,自然空气冷却难以满足其动力电池冷却需求,导致Nissan Leaf的电池包寿命大大衰减。
图2 (a) 采用自然空气冷却的锂离子电动汽车Nissan Leaf
因此,为保证高端快充电动汽车的长循环寿命,需要配置更高效的热管理系统。强制空气冷却是一种主动式空气冷却技术,借助外部能量促进空气流动从而增强了热传递。图2(b)和2(c)分别是自然空气冷却和配置了风扇的强制空气冷却示意图。
图2 (b) 自然空气冷却示意图;(c) 主动空气冷却示意图
相较于自然冷却,强制空气冷却效果得到了改善,但由于增加了风扇等散热器设备,噪音和能耗也会增大。空气的流动通道决定了空气流动方向和热量传递方式,可通过调整气流通道的形状来提高空气冷却BTMS的冷却性能。
空气冷却系统的气流流型有串行通风和并行通风两种,其中并行通风的空气冷却BTMS的均温性和冷却性能更优异。此外,电池布局也是影响冷却性能的重要因素。
Fan等的研究表明,空气冷却系统中电池对齐排列比交错或交叉排列能产生更好的冷却性能。早期储能电站一般采用强制空气冷却技术,如图2(d)安装了风机的空气冷却集装箱和图2(e)某空气冷却储能电站系统。对于这些储能电站,强制空气冷却技术可以有效降低温度,但在均温性方面效果较差。
图2 (d), (e) 主动风冷储能集装箱示意图
大量研究表明,空气冷却技术与其他冷却技术结合使用可以显著降低电池单体间的温差和整体温升,并能满足电池在较高充放电倍率(2~3C)下的冷却需求。
如Ma等提出的与二氧化硅冷却板相结合的空气冷却电池热管理系统,二氧化硅冷却板除了构建气流通道外,还可以作为散热导体,相比于传统的并联空气冷却电池模组,气流分布的均匀性得到提高,且电池模组的温差降低至1.84℃,电芯的平均温度也降低了10℃。
徐晓斌等提出的基于热扩散板的圆柱形锂离子电池风冷热管理系统,其电池模组的最高温度和最大温差分别降低了6.36和2.72℃,明显改善了降温能力和均温性。
Ren等将U形微热管阵列与主动空气冷却结合,结果表明,电池在2C恒流充电和3C恒流放电条件下的瞬时最高温度为51.70℃,单个电池的温差为1.14℃,即使以2C恒流或5C脉冲放电,电池系统的温度也能得到有效降低。
目前,在电动飞行设备领域,仍选择空气冷却作为首要冷却技术。空气冷却技术相比于液冷技术重量更轻,不会增加飞行设备的重量负担,且能耗更低,具体商业应用实例如图3所示。
图3(a)~3(c)展示的分别是某电动无人机,以及用于无人机中的空冷电池模组和软包锂离子电芯。无人机在工作时,空气从电池模组外壳风道进入模组内部与电芯进行热交换,从而降低电芯温度。
图3 (a) 某电动无人机;(b) 自然空冷电池模组;(c) 用于航模无人机的3.7 V软包锂离子电芯;
目前的电动飞行汽车采用的也是自然空气冷却技术,图3(d)~3(f)分别是某电动飞行汽车及其电池舱和自然空冷散热模组示意图,
(d) 某电动飞行汽车;(e) 碳纤维底座分散式电池舱;
图3(g)是用于电动飞行汽车的高能量密度全极耳软包锂离子电芯。
(f) 自然空冷电池模组;(g) 全极耳叠片高功率低发热率电芯
该飞行汽车的碳纤维复合材料底座与软包外壳的电芯均满足了轻量化要求,另外,风道与散热模组外壳一体化的设计在保证为电池散热的同时也不会增加重量负担。
综合来看,自然空气冷却更适用于这些对重量有要求的电动飞行设备,通过合适的风道设计还可以增大散热模组与空气的接触面积从而增强散热效果。
液冷是以液体为冷却介质,利用冷却液的相变或流动与电池系统的发热部件进行热交换的冷却技术,具有散热快、冷却效率高的优点。
一般将其分为直接液冷和间接液冷,直接液冷的冷却液与发热器件直接接触,如具有代表性的浸没式液冷。间接液冷的冷却液与发热器件不直接接触,而是在特定部件中流动间接冷却电池,如冷却板液冷。
冷却板液冷技术发展较为成熟,相对于空气冷却技术,其冷却效果明显提升,且冷却板的材质一般是铝及铝合金,成本较低。
目前,对于冷却板液冷系统的研究主要集中在冷却板结构、流体流动分布、冷却液通道几何和参数的优化上,旨在进一步简化制造工艺,增强均温性和冷却性能。
近年来关于冷却板液冷技术的优化策略,优化重点主要集中在冷却液通道结构和冷却液流动方向两方面。
陈雅等基于传统的蛇形流道进行了通道优化,设计了一种新型二次流蛇形液冷板,如图4(a)所示。
图4 (a) 锂离子软包电池的二次流蛇形通道冷却板示意图;
通过数值模拟仿真发现,新型二次流蛇形液冷板的压降比传统液冷板大幅降低,节省了泵功,且随着冷却液流速的增大,液冷板的最高温度和最大温差均逐渐减小。在流速超过0.4m/s后,温度和最大温差基本不变,其中最大温差可保证不超过4.5℃。
Zuo等则研究了冷却液不同的流动方向对冷却效果的影响,如图4(b)所示,在方形LiMn2O4电池的前后两面紧贴着两个微型U形通道冷却板,设计了U形通道的入口布置在同一侧和不同侧两种冷却方案,结果表明,两种方案下的电池最高温度基本相同,但当采用U形通道的入口在不同侧的设计方案时,电池温度分布更均匀,且在2~3C较高放电倍率下具有更明显的冷却效果。
图4(b) 方形LiMn2O4电池的微型U型冷却板示意图;
除此之外,在有限的冷却板空间中通过合理的结构设计来增加液体的流动通道也是主要的优化策略之一。Zhao等设计了一种基于方形LiFePO4电池的蜂窝结构冷却板,如图4(c)所示,密集的蜂窝通道显著增加了冷却通道。
图4(c) 方形LiFePO4电池的蜂窝状流道冷却板示意图
数值模拟结果表明,冷却通道宽度为3mm,正六边形铝块中心到边长的垂直距离为6.8mm是最佳的结构参数,该参数下的最大温差不超过4.1℃,且当冷却液以相反方向在相邻的蜂窝式液体冷却板中流动有更好的均温效果。
上述研究表明,通过合理的冷却液通道结构设计可以增加冷却液与电池的接触面积,从而调控散热效果,同时冷却液的流动方向也对均温性至关重要。
目前,冷却板液冷技术已经成功应用于储能电站和电动汽车等领域,图5展示了某公司的冷却板液冷产品及相关专利。
图5 (a) 冷却板液冷电池舱;(b) 冷却板液冷电池包及内部结构简图;(c) 冷却板液冷组合式储能电池柜;(d) 冷却液循环管与电池板的安装结构示意图
其中,图5(a)和5(b)展示的分别是冷却板液冷电池舱和冷却板液冷电池包,所对应的内部安装示意图如图5(c)和5(d)所示。电池两侧均与冷却液循环管接触,从而高导热、高比热容的冷却液间接式进行对流换热,实现快速降温,且减小了电芯温差。鉴于冷却板液冷技术的冷却效果,许多电动汽车的电池热管理系统也采用了该技术。
特斯拉4680CTC电池包[图6(a)]的内部冷却板[图6(b)]采用了蛇形设计,增大了与圆柱形锂离子电池之间的接触面积,冷却效果得以进一步增强。
图6 (a), (b) 特斯拉4680 CTC电池包及电芯间蛇形冷却板示意图;
图6(c)和6(d)是某公司麒麟电池包与冷却板的组装示意图和结构图,冷却通道集成在箱体上盖与下箱体之间的加强体中,提高了空间利用率。
图6(c), (d) 某公司麒麟电池包及冷却板安装示意图;
图6(e)展示的是某公司刀片电池车身一体化(CTB)电池包,冷却板组件[图6(f)]贴合在电芯上方,由均温板、冷却板和基板构成,均温板与冷却板的协同作用能够很好地控制电池包的温度和温差。
图6(e), (f) 某公司刀片CTB电池包及冷却板组件示意图
结合上述分析,可以看出冷却板液冷技术实现了很好的商业应用,但为了充分利用空间或增强散热效果,需要根据电池的形状对冷却板的形状进行合理设计。
综合而言,冷却板液冷对于大部分应用场景来说是一种比较有效的冷却技术,其关键构件冷却板一般由铜、铝等热传导材料组成,成本不会过高,适宜用在电动汽车或其他对冷却效果有更高需求的设备上。
浸没式液冷技术是指将电池及发热部件直接浸没在绝缘的冷却液中,省去了风扇等散热器,降低了能耗和噪音,是一种均温效果更好的电池冷却技术。
常用的浸没式液冷冷却液有绝缘油和氟化液两种,成本较高。由于冷却液的存在,浸没式液冷系统的重量和体积较大,不宜应用在移动运行的电动汽车中。
由于储能电站对电池热管理系统的体积要求较低且一般不需要移动,故更适合采用浸没式液冷技术,有相关报道表明,采用浸没式液冷的电池储能系统可确保电池运行过程中的平均温升不超过5℃,单体电池间的温差不超过2℃,能够有效延长储能电站的使用寿命,提高安全性。
图7展示的是一些以绝缘油为冷却液的浸没式BTMS的相关研究。如图7(a)所示,Wang等采用高绝缘10号变压器油作为浸没冷却剂,设计了一种用于三元锂离子软包电池的新型浸没式液冷BTMS,并研究了影响油浸式BTMS冷却性能的因素。
图7 (a) 三元软包锂离子电池组油浸式液冷BTMS及结构示意图
结果表明,增加浸没深度可以扩大接触表面积,提高传热系数和冷却效果。与自然空气冷却的情况相比,电池模组的最高温度和最大温差分别降低了32.4%和75.3%,其中最大温差为1.23℃,BTMS的冷却性能得到了极大改善。
张进强等的研究发现,绝缘油的流动方式对BTMS的冷却效果也有影响,图7(b)是该研究的实验原理图以及4种不同的绝缘油进出口方式示意图。
图7 (b) 小型NCM811动力电池油浸式液冷BTMS原理图及4种绝缘油进出口方式示意图
实验中作者对油浸没量、环境温度、流量及流动方式对冷却性能的影响进行了分析,结果表明,在1.5C倍率下充电时,油浸没量(BTMS中油的体积Vo与电池模组体积Vb的比值)为0.2,0.5和1时对应的电池模组最大温差分别为2.6,3.1和2.8℃,明显低于空气自然对流时的最大温差(7.2℃)。
在高充放电倍率或较高环境温度下,绝缘油采用流动方式4(异侧上进下出)展现出了比流动方式2(同侧上进下出)更好的冷却和均温性能,1.5C放电倍率下采用流动方式4的电池模组最大温差为3.6℃,远低于流动方式2下的最大温差(10.5℃)。
为了进一步提高油浸式冷却系统的散热性能,Liu等设计了一个变压器油浸没式电池热管理系统模型,如图7(c)所示。
图7(c) 18650 LiCoO2电池的油浸式液冷实验示意图和电池在不同冷却条件下的温度曲线
在2C放电倍率下,采用油浸式冷却的电池最高温度和最大温差分别为37.35和2.64℃,远低于采用自然冷却的电池。实验中测试并分析了绝缘油在3~50mL/min体积流速下的冷却效果,确定15mL/min为最佳体积流速,在该流速下电池的最高温度低于30℃,且电池表面平均温差仅为1.31℃。
上述研究结果表明,浸没式液冷是一种可有效降低电池温升和温差的冷却技术,通过对冷却液的浸没量、流动方式和流动速度等参数进行优化,可以在1.5~2C等较高倍率下将电池温差基本控制在3℃及以下。因此采用浸没式液冷的储能电站能够表现出更长的使用寿命和更高的安全性,且浸没式液冷也更有利于体积较大的单体电池传热。
通常,根据冷却液是否发生相变,可将浸没式冷却分为单相浸没式冷却和相变浸没式冷却,所对应的循环流动示意图见图8(a)和8(b)。
虽然浸没式液冷的研究起步较晚,但已成功应用在储能电站中,另外,部分电动汽车也开始尝试采用浸没式液冷技术,如图8(c)展示的以绝缘油为冷却液的电动汽车。
图8(d)和8(e)为某大型储能电站及所使用的液冷储能系统。
以及图8(f)某汽车公司发表的用于电动汽车的完全浸没式电池冷却系统的专利示意图。
相较于冷却板液冷技术,浸没式液冷技术的均温效果显著,但其对冷却液的绝缘性以及对电池热管理系统整体的设计也提出了更高的要求。从当前浸没式液冷技术的应用情况来看,浸没式液冷已经得到了广泛的认可,在不久的将来可能会成为大型储能电站的主流冷却技术。
但是浸没式液冷的成本较高,难以在电动汽车和小型电子设备中实现大范围的应用。对于一些冷却要求更高的高端车型来说或许会采用浸没式液冷技术。目前浸没式液冷技术尚处于初始商业化阶段。
基于相变材料的电池热管理系统(PCM-BTMS)是一种利用PCM储存和释放潜热使电池组维持在最佳温度的被动热管理系统,具有不消耗能量、无运动部件、维护成本低等优点,且在维持电池表面均温性方面具有巨大优势。
目前,用于电池热管理的PCM主要包括有机材料(石蜡、烷烃、有机酸)、无机材料(水溶液、盐类水合物和熔融盐)和共晶材料。但是纯PCM存在热导率低的问题,需要加入导热增强材料使用,如泡沫铜、膨胀石墨、纳米颗粒等,这些材料大多能同时解决PCM导热系数低和相变后流动的问题。
图9展示了最近几年关于相变材料冷却锂离子电池的研究案例。如图9(a)所示,Zhang等将月桂酸(LA)和石蜡(PA)的混合物与膨胀石墨(EG)结合,制备了复合相变材料(CPCM),LA和PA的混合物提供潜热,EG增强导热性。用CPCM冷却软包聚合物锂离子电池,电池的最高温度可降至42.39℃,相应的温差在±1℃,且当该CPCM经过100次加热和冷却循环后,仍具有较高的潜热特性。
图9 (a) 采用复合相变材料冷却的软包锂离子电池
杜江龙等提出了一种CPCM与空冷结合的圆柱形(26650型)LiFePO4电池组散热结构,如图9(b)所示,并使用COMSOL多物理场对该模型进行了数值模拟,结果表明,CPCM结合空气冷却的复合式BTMS具有更好的散热性能,电池表面的平均温度降低约11℃,最高温度降低约4℃。
图9(b) 圆柱形LiFePO4电池的CPCM/空冷复合式散热模型
另外,采用双向通风方式比单向通风方式的降温效果更显著。图9(c)是An等提出的CPCM与水冷相结合的紧凑型混合热管理系统,该复合式BTMS具有最优异的散热性能,可以将电池模组的最高温度和温差分别控制在46.21和3.5℃。且当CPCM厚度为3mm、内径和外径分别为16和19mm、微通道层数为4的条件下,可以将CPCM的温差和液相分数控制在合理的范围内。
图9(c) 26650锂离子电池的CPCM/液冷复合式散热模型
目前,PCM散热系统已经在某四座电动飞机上得到应用,如图10(a)所示。
图10 (a) 某四座电动飞机
该电动飞机由高能量密度航空型动力锂离子电池[图10(b)]提供电源,
图10 (b) 某动力锂离子电池
电芯之间通过均热片减小温差[图10(c)]。
图10(c) 软包电芯和均热片组合示意图
该均热片是一种柔性导热/储热双功能复合材料,专利示意图如图10(d)所示。
图10(d) 新型纳米储热相变材料
相变储热材料作为分散相以小颗粒的形式均匀分布在高导热基体中,加快了相变储热成分的响应速度。PCM质量较轻,应用到电动飞机上不会增加重量负担,但由于其成本相对较高,应用受到了一定程度的限制。
在实际应用中,PCM一般需要与其他冷却技术组合使用来增强冷却效果,如结合较大传热面积的翅片提高散热量,并且翅片的某些结构还可以作为支撑PCM的骨架来弥补PCM的流动缺陷。
另外,还应考虑PCM是否符合应用场景的要求,其熔化温度必须在电子元器件的工作温度范围内,且无腐蚀性、易燃性和爆炸性等,PCM的厚度也是影响冷却性能的关键参数。目前,PCM尚处于初步应用阶段,下一步还需要对其结构进行优化以减少相变过程中的体积变化,或开发新型的封装技术以降低其泄漏风险。
热电冷却技术是一种基于珀尔帖(Peltier)效应的新型主动式冷却技术,当有直流电通过时在一侧吸热在另一侧放热,从而实现空气或液体的冷却。热电冷却技术有很多优点,如无制冷剂污染、驱动电压低、制冷启动快、稳定性好、噪音低、没有运动部件和内部化学反应等,但也存在冷却效率低、难以将半导体材料加工成大面积器件等问题。
为了使热电制冷技术成功应用于锂离子电池热管理系统中,研究人员进行了大量研究。Li等提出了一种结合铜网的双二氧化硅冷却板与风冷的复合冷却系统,如图11(a)所示,通过实验和模拟发现,在放电过程中电池的最高温度会随着二氧化硅冷却板厚度的增加而降低,并确定1.5mm是二氧化硅冷却板的最佳厚度。
图11 (a) NCM软包电芯双面半导体铜网复合散热系统
单春贤等则采用了将热电冷却与液体冷却耦合的方式,如图11(b)所示,将热电冷却器装配在电池底部并与液冷组件相连,在各接触面均粘贴了导热硅胶垫片,后使用磷酸铁锂电池对该电池热管理系统的可行性进行了验证,结果表明,增大冷却液流速或降低其温度,均可提高热电元件的制冷性能。不同放电倍率工况下,采用热电液冷复合冷却方式后动力电池组均获得了较好的工作效果。
图11(b) LiFePO4电芯底部TEC制冷与液冷板复合热管理示意图
为进一步探究基于热电冷却的冷却系统对动力电池的冷却效果,李俊伟等构建了热电制冷器(TEC)两侧对称布置的热电制冷系统,并在由18650圆柱电池组成的电池模组内部填充复合相变材料以提高导热性能,采用液冷散热器对TEC热端进行散热,如图11(c)所示。
图11(c) 基于TEC的复合散热结构及TEC实物图和示意图
结果表明,TEC的冷端和热端温度、制冷功率均受TEC电流影响,且冷、热端热阻也会影响TEC的制冷功率和最佳制冷电流。
在上述研究中,TEC均与其他冷却技术结合使用,考虑到TEC的制冷效果较差且难以加工成大面积器件,故热电冷却技术比较适合应用于小型电子器件中,不适合在大型电动设备上应用。
目前,TEC制冷也实现了初步商业化,图12展示了TEC在手机散热器中的应用实例。TEC冷端与电池直接接触,转移电池的热量,并在热端与金属铝、铜网、液冷板和PCM等多种导热模式复合,最终使热量散去。
图12(a)中的TEC结合了空气冷却技术,通过太阳花形状的金属散热鳍片增大了散热面积,增强了冷却效果。
图12 TEC手机散热器:(a) 10 W不插线TEC+铝合金金属鳍片+风扇空冷
图12(b)中的散热器采用的是双核TEC、铝合金制冷面板和散热风扇的复合方式,铝合金制冷面板负责传递热量,并最终由风扇将热量散出。
(b) 双核大面积TEC+铝合金+空气冷却散热器;
图12(c)中的散热器则采用了TEC与循环水冷板相结合的方式,在提高冷却性能的同时,也增强了均温性。在上述这些应用中,TEC均结合了其他的冷却技术,从而增强了冷却效果。
(c) 单核TEC+循环水冷板
基于目前对热电制冷复合热管理技术的研究可以发现,热电制冷与其他散热方式耦合的复合散热系统将是TEC实现大规模商业化应用的基本方式。如TEC与液冷结合,可实现快速制冷,提高均温性。另外,还需要在TEC的制造工艺方面继续探索,以降低TEC的制造成本。
二、BTMS的模型模拟
热模型是优化电池热管理系统设计的有力工具,随着计算机科学技术的发展,开发了更简单高效的锂电池仿真软件,如COMSOL多物理场、ANSYS Fluent等。利用这些软件可以建立有效的电池热模型,从而预测电池、模组和电池组在各种充、放电循环下的温度分布。常见的锂离子电池产热模型主要包括电-热耦合模型和电化学-热耦合模型。
电-热耦合模型结合了电池等效电路模型和热等效电路模型,可以在电池工作过程中同时评估电池SOC和内部温度。
电化学-热耦合模型是基于电池的电化学反应和传热特性建立的,已从一维模型发展成为适用于更多场景的三维模型。
电化学-热耦合模型考虑了电池内部的电化学反应产热,具有更高的计算精度,如基于多孔电极理论所提出的LiFePO4/石墨烯锂离子电池电化学-热耦合模型,用于研究基于PCM的18650锂离子电池冷却系统热性能的电化学-热耦合模型,以及描述实际驾驶过程中电动汽车锂离子电池组电化学热分布的双向耦合电化学-热模型等。
Zhai等基于电化学-热耦合模型,模拟并分析了圆柱形锂离子电池在1C放电倍率下的热行为和热应力分布,电池在不同放电时间下的温度分布和热应力分布如图13所示。电池温度在放电的早期和晚期迅速升高,在放电中期,电池温升比较缓慢。电池应力的变化趋势与温度的变化趋势一致,在放电早期和晚期迅速增加,在放电中期缓慢增加,且电池中央部分的应力远远超过最外面部分的应力。
图13基于电化学-热耦合模型模拟得到的电池(a)温度分布和(b)热应力分布
目前的三维电化学-热耦合模型需要大量算力,需对其进行简化从而降低计算成本。另外,将电化学-热耦合模型与其他模型结合,可用于描述电池在工作过程的多场耦合特性。
如与机械模型耦合,可以分析应力对锂离子电池容量衰减行为的影响。随着互联网科学技术的进步,锂离子电池的热管理也逐渐向智能化、网联化、一体化的方向发展,多物理模型与预测技术相结合将是电池安全研究的最新趋势。
精确的电池热管理技术对于锂离子电池的大规模应用是非常重要的,高效、环保和低成本将是未来电池热管理冷却技术的发展趋向。高效的BTMS应具有精确度高、状态的实时可预测性和可控性,现有的仿真模拟软件为更好地开发电池热管理技术提供了强大支撑。
根据文中对空气冷却、液体冷却、相变材料冷却及热电冷却技术的讨论,作出以下结论和展望:
(1)空气冷却作为一种传统的电池热管理技术,已难以满足高功率锂离子电池组的热管理需求。可以预测,将来在大型储能电站和动力锂离子电池领域,空气冷却会被冷却效果和均温性更好的液冷技术取代。
(2)液冷技术可分为直接液冷和间接液冷,其中,冷却板液冷技术发展较为成熟,在一些储能电站和电动汽车中都实现了应用。浸没式液冷目前正处于初步商业化阶段,能表现出更好的冷却和均温效果。在应用场景方面,浸没式液冷技术将会更多地出现在大型储能电站和高端电动汽车中,而对于大部分电动汽车和小型储能电站来说,更适合采用冷却板液冷技术。
(3)PCM在相变过程中具有较高的吸热和蓄热能力,无移动部件,结构更灵活,非常适合用于电子设备的热管理。但是,由于纯PCM导热性较差,往往需要加入价格较贵的导热增强材料,限制了其在大型电池热管理中的应用。
(4)热电冷却技术作为一种新型冷却技术,冷却响应快、无冷却液泄漏问题,已经在手机等设备中实现了商业化应用,但由于其冷却效率低,在实际应用中需要结合其他冷却技术。为扩大其应用范围,下一步还需要在提高冷却效率、降低成本等方面继续优化。
总体而言,现阶段仍没有十分完美的冷却方案,可以根据不同冷却技术的优缺点来选择合适的热管理技术进行组合,以满足不同用户的需求。
参考资料:李嘉鑫,李鹏钊,王苗,等.锂离子电池热管理技术研究进展.过程工程学报
储能液冷系统交流群
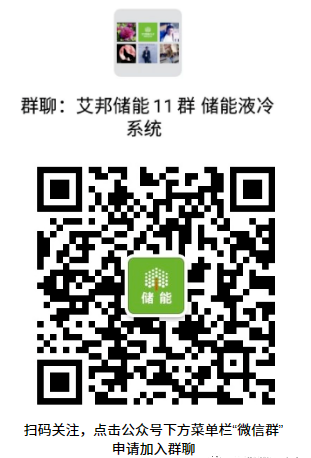
活动推荐:2024年液冷储能系统与消防安全论坛(3月21日 苏州)
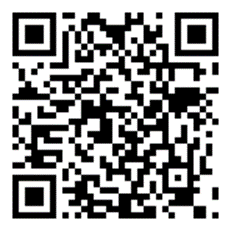
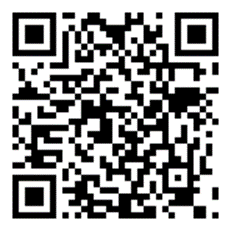
推荐阅读
原文始发于微信公众号(艾邦储能与充电):锂离子电池热管理技术研究进展